Business leaders explore how lessons from today’s supply chain challenges will mould a more sustainable approach for US corporates.
What happens when you turn off the world’s supply chain … and then turn it back on again?
Over the last two years, the Covid-19 pandemic has exacerbated a number of structural vulnerabilities in global supply chains that have been building for decades. With disruptions becoming the new normal, US companies across a variety of sectors are focusing on redesigning their supply chain strategies to promote resilience and agility.
In mid-February, business leaders from FedEx Logistics, General Motors and the US Chamber of Commerce gathered to explore the genesis of today’s supply chain crisis, and discuss ways to build a more sustainable supply chain in the future. The virtual conference, Banking in a Changing World: Managing Supply Chain Disruptions from ‘Just in Time’ to ‘Just in Case’, was hosted by BNP Paribas, prior to the conflict In Ukraine.
A challenge years in the making
Panellists noted that the problems facing global supply chains are a direct result of more than two decades of flawed trade policies, persistent offshoring and under-investment in critical infrastructure in North America. The pandemic has since exacerbated existing pressures, but so has the subsequent economic reopening.
In addition to pent-up consumer demand fuelling product shortages, supply chain bottlenecks have become endemic due to a number of significant events. The flight restrictions resulting from the Ukraine crisis are the latest in a series of disruptions that have included a fire at the largest semi-conductor factory in Japan, extreme weather triggering further semi-conductor shortages in Taiwan, the record freeze in Texas, a stranded container ship blocking traffic in the Suez Canal, and destabilising border protests in Canada.
At the same time, efforts to improve supply chains are facing a number of societal challenges, principally inflation and rising wages caused by labour shortages. With the recovery timeline hard to predict, governments are intervening through various policy initiatives to contain the wider economic fallout. The nature of supply chains are evolving as a result of these ongoing crises, complex geopolitics and industry transformation.
Building a more secure US supply chain
The pandemic has shifted the primary driver of corporate supply chain strategies from cost to resilience, especially as board executives, shareholders and regulators make supply chain management a priority. For example, the Biden Administration’s American Supply Chain Executive Order is reviewing weaknesses in US supplies of vital technologies, metals and pharmaceuticals, which could have serious knock-on effects for domestic businesses.
In response, corporates are increasingly moving away from the traditional ‘Just in Time’ supply chain model towards a ‘Just in Case’ philosophy. They are doing so by building up deeper stock inventories to mitigate potential product shortfalls and simplifying operations through on-shoring or near-shoring activities that were previously offshored to low-wage countries. Elsewhere, some corporates are embracing the concept of vertical integration, whereby a company engages directly with key component suppliers across the chain to give them greater autonomy or visibility over production and logistics.
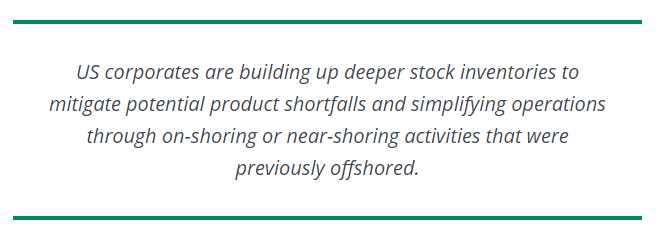
The emphasis on supply chain security is made even more urgent by the current shortage in semiconductors, which is having huge ramifications across a number of industries – most notably automobile production as manufacturers transition to electric vehicles (EVs). The US government is conscious of the challenges posed by such a shortage, which is why it passed the US$52 billion CHIPS for America Act in 2021, a subsidy programme to expand domestic production of semiconductors.
However, as demand for EVs is expected to grow exponentially, manufacturers will need to procure more critical minerals and rare earths for battery production. The US does not have the capabilities or resources to obtain all of these materials domestically, so alternative sources will need to be identified. Instead of being wholly dependent on a single country for these commodities, the domestic auto industry must diversify its sources of rare earth supplies across multiple markets (a situation further exacerbated by the Ukraine-Russia crisis, which is impacting commodities from minerals to agriculture).
Modernising US infrastructure
One panellist noted that investment into core infrastructure in North America has lagged other markets, as roads, railways and ports struggled to cope with the fallout from the pandemic. The scale of the problem was underlined by one panellist, who noted that the Port of Los Angeles – the largest port in the US – is now ranked 17th in the world by shipping traffic volume (throughput), putting it well behind many of the leading Chinese ports.
Another panellist noted that, in contrast to other major economies such as China, the US has not made infrastructure investment a priority; as a result, it is highly vulnerable to supply chain shocks. Nonetheless, the US government has awakened to the scale of the problem, earmarking approximately US$17 billion for investment into modernising infrastructure at domestic ports and waterways as part of the bipartisan Biden-Harris Port Action Plan. The proposals also envisage the greater use of public-private partnerships to stimulate infrastructure development, an investment approach that has historically been muted in the US compared with other markets.
Resilience is no longer a buzzword
Supply chain weaknesses have been a recurrent problem facing the global economy for more than two decades, although the pandemic was a wake-up call for many corporates. The deficiencies of the ‘Just in Time’ supply chain model were woefully exposed by the pandemic and other recent challenges, forcing corporates to rethink their supply chain models. Resilience is now the main factor shaping supply chain strategies in the US and globally.